
Old solder should be removed and replaced with new solder whenever a component is reattached.

Solder needs to remain ductile in order to absorb the stresses of expansion and contraction caused by heating and cooling. Every time that solder is reheated, the molecular structure tends to become increasingly brittle. Reheating solder three or four times - even with the addition of flux - may affect the physical composition of the metals. If it becomes part of the new solder joint, it will have been heated at least three or even four times. That solder has already been heated twice.
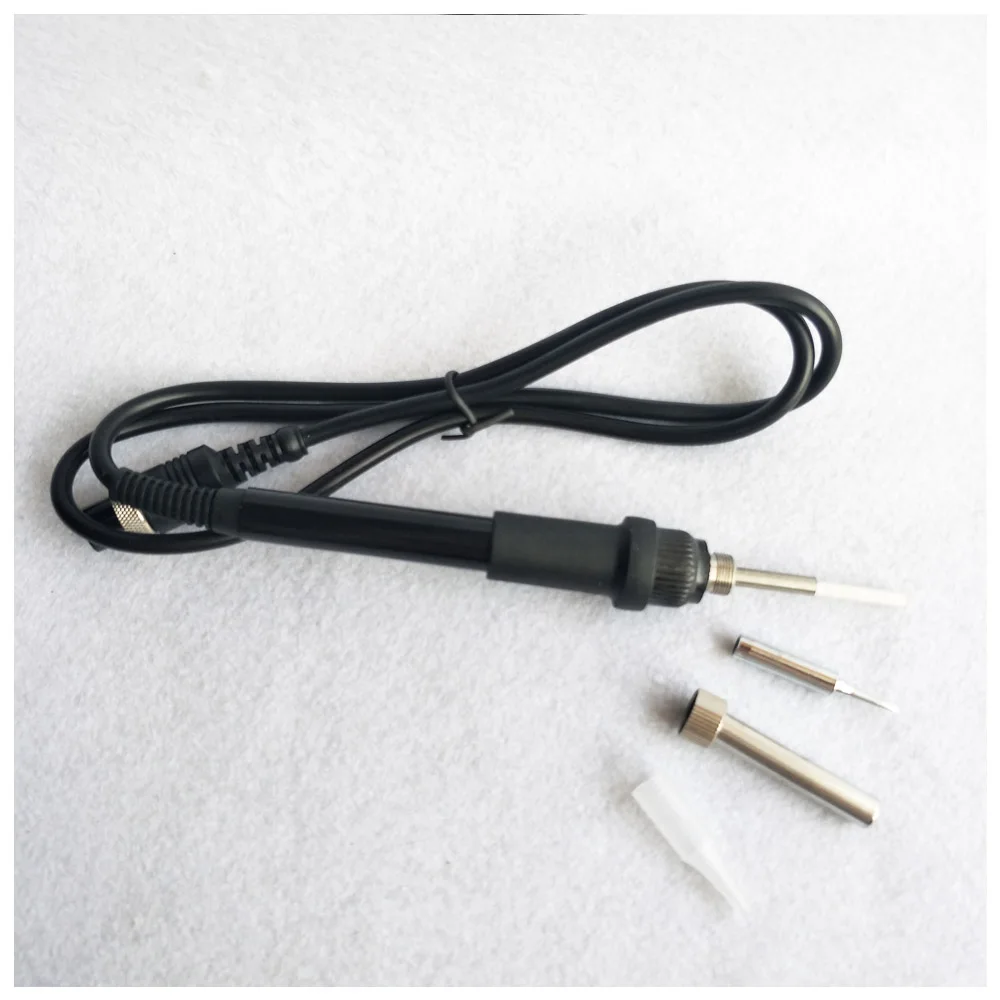
If the tip extends too far beyond the edges of the joint, it could come in contact with another component or the surface of the circuit board. The outside diameter of the tip should not cover the pad completely or touch the circuit board base material or solder mask. The smallest tip should be selected, providing that the tip fits over the component lead and allows room for molten solder and air to pass through it. Larger tips with more surface area will transfer heat faster than smaller tips. The size and shape of the component removal tip will have an effect on the rate of heat transfer. Where possible, the width of the soldering iron tip should be slightly smaller than the width of the pad. While there is no exact rule about how the size of a soldering iron tip should compare to the size of the termination, if the tip extends too far beyond the edges of the joint, it could come in contact with another component or the surface of the board. Tip size is based on the size of the component.
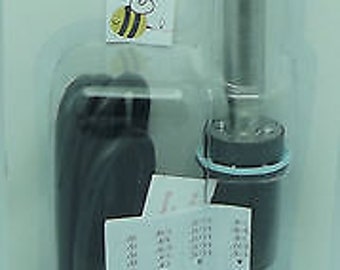
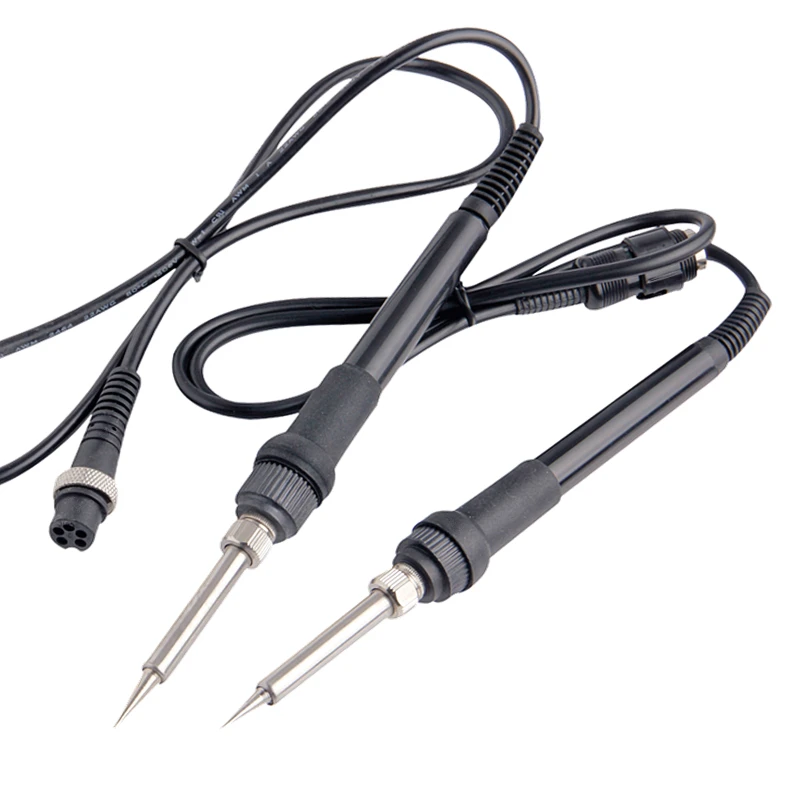
The size and shape of the soldering iron tip will have an effect on the rate of heat transfer. Figure 3: Remove excess solder from surface mount pads using a vacuum desoldering tool.Ĭaution: Silicon based lubricants or hand creams should not be used on or near surfaces to be soldered.
